WHEAT TO FLOUR
In the mills's early
years, wheat was brought to the mill by horse and wagon in bags
and was left at the mill until the milling was finished. |
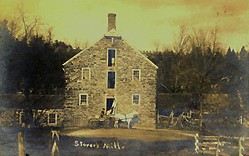 |
Bags of wheat were unloaded on the main
floor, weighed, and then dropped down a chute to a bin in the
basement. Stored wheat was sent to the second floor. Wheat made
into flour was elevated from the receiving bin in the basement
to the main floor . A wheat cleaner in the basement used screens
to remove straw, stones and other debris.
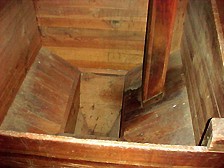 |
The wheat was elevated
to large bins on the second floor directly above the millstones.
A slide was opened at the bottom of the bin and the wheat dropped
down a spout to the hopper of the millstone. |
After grinding on the
millstone the flour was elevated to the flour sifting machine
on the third floor. It was separated into flour, middlings, and
bran. |
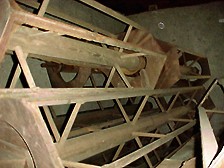 The sifting reels piled at the Stover-Myers Mill in
this picture have no mesh on them. |
 |
|
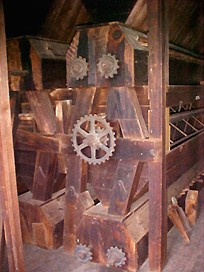 |
Another Stover Mill
in Erwinna, PA along River Road at the Delaware River is similar in design
to the mill in Pipersville. This mill has the sifting equipment in place,
Though many of the silk fabrics are damaged. |
|
A wooden structure supports
the sifting reels and allows them to turn (on the third floor of the Stover
Mill in Erwinna, PA). |
This wooden flour sifting
machine on the third floor is made of pulleys, wheel, sprockets,
belts and chains. The main wooden wheels are about eight feet
long and 2 feet in diameter. The three sections of the machine
were covered with silk of different gauges (tightness of the
fabric weave). |
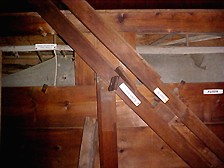 |
Here a view into the reel box allow
us to see the silk in place (off-white color) on some reels. |
|
Ground wheat would pass through the reels
as they turned and flour would pass through the fine section.
Middlings or low grade flour came through a coarser section. The
bran or outside shell of the wheat was sent through the last section.
The grain products were moved along until they came out of a spout.
Later, during the roller mill period, gyrators
were used to sift the flour. In the mill the gyrator system can
still be seen.
The products were sent down separate chutes
to the second floor and stored in bins.
CATTLE FEED
Grinding corn and other grain for cattle
was a much simpler process than making flour.
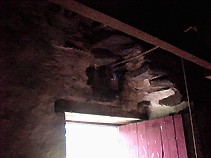 |
|
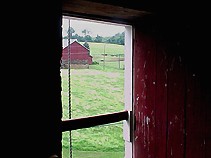 |
Corn cobs were pulled
up to the third floor using a hoist. |
|
A rope was suspended
from the front of the mill roof and using ropes, the corn was taken from
the wagon in bags to the third floor door. |
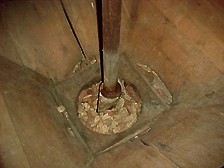 |
|
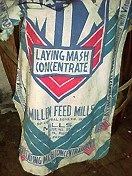 |
The corn
was dropped in the cob crusher. It was crushed into small enough pieces
to go through the millstones |
|
The product
was then bagged for use as animal feed. |